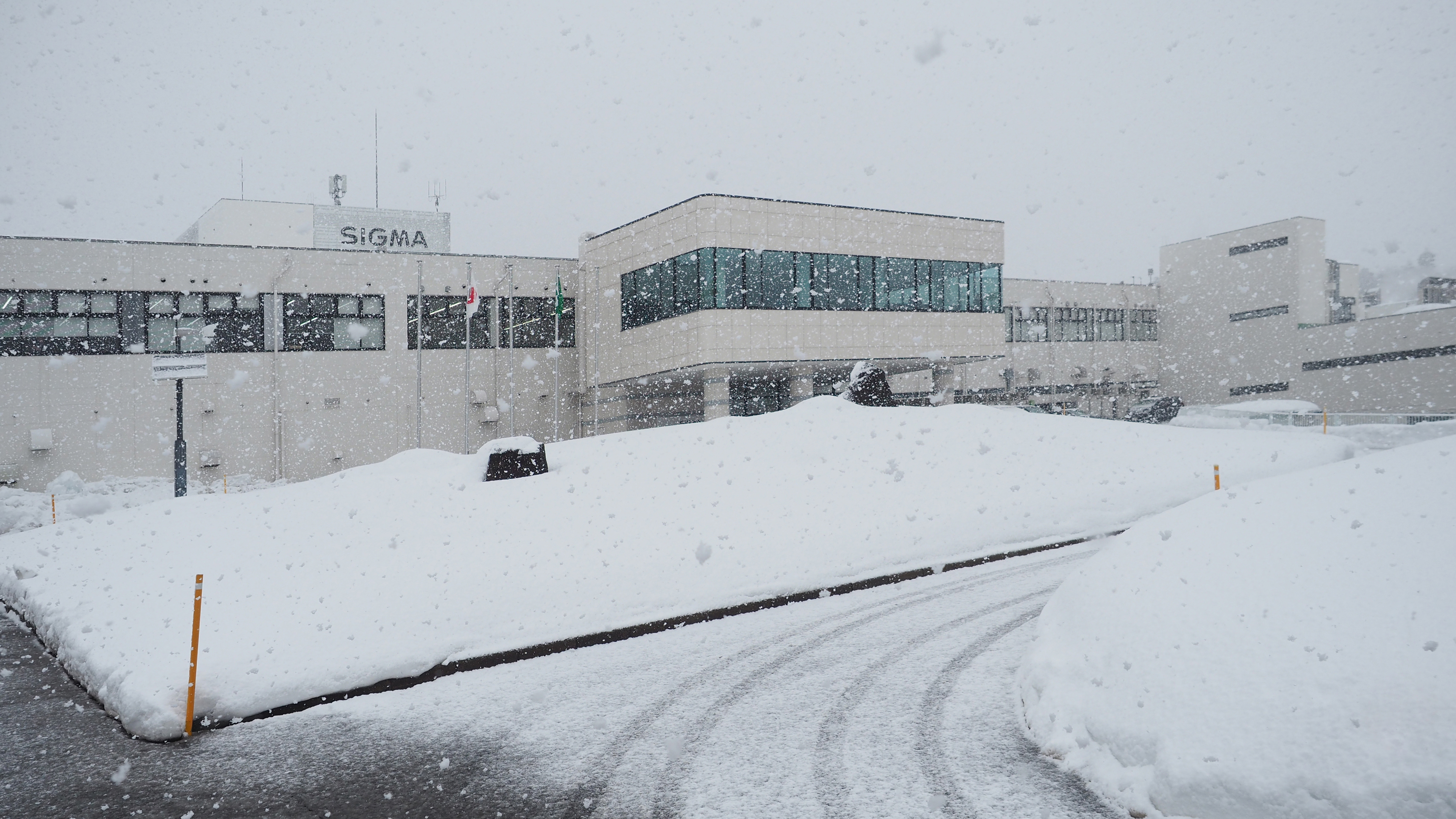
Earlier this year, myself and Digital Camera World's Editor in Chief, James Artaius, were invited to Japan by Sigma to see three brand new products: the Sigma BF full-frame camera, and the Sigma 300-600mm f/4 DG OS | S and Sigma 16-300mm f/3.5-7.1 | C zoom lenses.
As part of the trip, we were also invited to Sigma’s one and only factory in the mountainous region of Aizu, where we were treated to a brilliant tour of the factory to see how the company manufactures all its lenses and cameras in-house from start to finish.
The grand tour begins!
Before we could begin, it was important to put on shoe coverings and lab suits to avoid any contamination. One of the main mottos of the assembly division is to not bring dust into the environment, so some workers have to pass through air showers before entering clean rooms within the factory.
First up was the Production Engineering & Development Divisions, where Sigma's production and development engineers can work and communicate freely and easily.
Next up a quick walk past the Prototype Jigs & Tools Processing Division, where parts for prototypes are machined for the engineers to work through any teething problems, and identify any defects before the molds and dies are finalized for mass production in the Mold & Die Manufacturing Division.
Each mold can take between six to eight weeks to finish and the division creates roughly thirteen resin molds and eight press dies on average per month. Sigma’s smallest mold weighs a hefty 100kg, while many weigh over a ton!
Metal Processing
Onto the Metal Processing Division, where around 15,000 parts are processed per day by 200 machining tools using aluminum, brass and stainless steel. The parts produced in this division are for camera bodies, lens barrels and even small electrical contact pins, and have super strict tolerances from +/-0.003 to 0.005mm (which is 10 times thinner than a human hair!).
Get the Digital Camera World Newsletter
The best camera deals, reviews, product advice, and unmissable photography news, direct to your inbox!
Also in the Metal Processing Division, Sigma was eager to show off its latest addition – several five-axis CNC machines installed specifically for the new Sigma BF camera, which is machined out of a single block of aluminum.
This is loaded and unloaded by automated robots and then taken to the next machine for further processing. The total process takes seven hours for each camera!
Plastic Fantastic
Next up, the Plasticity Division! Plasticity doesn’t just relate to plastic, though; this division encompasses everything from injection molding to metal pressing and stamping, painting, electroplating and even printing.
We caught a glimpse of Sigma’s impressive machines that create the plastic injection molding, with the company storing 1,500 molds ready to use in the process to create plastic components, and we saw them live in action creating the brand’s iconic lens caps.
No less than 38 machines are used to produce the plastic components using materials such as engineering plastic (EP) and thermally stable composite (TSC).
Resin granules are dried in a hopper at high temperatures, then melted down at around 572°F / 300°C and injected into the mold, where they re-solidify into the designed shape. Excess plastic is removed and ground up to be recycled.
Onto Metal Pressing & Stamping, and here dies are used by high-powered machinery to stamp or press out metal parts such as diaphragm blades, washers, clips, pins, metal guides and more. The materials used in the division include stainless steel, iron, aluminum, copper and brass.
There are two types of die: Progressive Die, which uses multiple pressing processes in sequence to create the final part from the metal material. Not only cuts, but also bends, and “punches”. Then there’s the Single-Shot Die, which creates the part in a single shot.
A lick of paint
The Painting Division is responsible for improving the surface properties of materials, mainly to enhance hardness, wear resistance, lubrication, corrosion resistance, oxidation resistance, heat resistance, insulation, and decorative and aesthetic qualities.
The division uses five different types of machines to carry out various types of painting, including an advanced twelve-axis machine that can closely mimic human-like movements.
We also took a pit stop at the Printing Division, where we saw machines printing the lens information found on the exterior of the lens, such as logo, focal length and f-values. This is mainly done by Pad or Silk Screen printing. Some Sigma lenses and cameras also require color inlay, which is a delicate process and needs to be done by hand.
A Sigma representative told us, “Since almost all printing here is visible from the exterior of the lens, the attention to detail is of utmost importance to create high-quality products”.
Next it was onto the Electroplating Division, where we saw components being electroplated and anodized. In the electroplating process, brass, iron, steel, phosphor bronze and zinc materials are treated with nickel and nickel-chrome plating to improve abrasion resistance, corrosion resistance, and lubricity improving durability and appearance. The anodizing process is similar, but creates an alumite coating on aluminum materials.
We witnessed first-hand Sigma lens bayonets being electroplated, with Sigma’s chief of customer service, Jonathan Ryan, telling us, “We believe that a beautifully coated and unadulterated bayonet helps to make a strong first impression when users first open up the lens box and take out their new lens”.
Glass Molding
Now onto the Glass Molding Division – the area that creates the magical glass that goes inside a Sigma lens.
This division molds special aspherical lenses from glass gob (a measured amount of molten glass cut from a stream of glass and fed into a molding machine) or blows it into a pre-form, with the melted glass taking on the desired shape and setting once cooled.
Sigma produces spherical lenses as well, with grinding and polishing processes which we will see later, but these aspherical lenses can suppress aberrations and improve optical performance and they are an essential key factor in increasing design freedom.
One of Sigma's major strengths is its ability to produce large-diameter aspherical lenses with diameters in excess of 80mm, which are used in ultra-wide-angle lenses. Sigma told us that 70 machines are used to produce 10,000 pieces per day.
The molding machines perform three processes: preheating, pressing, and cooling, reaching temperatures of up to 1,292°F / 700°C with pressures of 500-1000kg being applied to mold the lenses. It takes a minimum of 20 minutes to mold a single lens, with the longest taking about 2.5 hours.
Onto the Ultra-Precision Machining (GM Molds) division now, and this is where the molds for the GM division are manufactured. The Glass Molds use three main processes: rough machining, finishing machining and hand polishing.
Each mold is made of tungsten carbide and is much heavier than it looks; a 4cm cube weighs around 1kg! These molds are used to make aspherical lenses, so their precision is highly important for creating ultra-refined aspherical lens elements.
Processing and fitting the lenses
As you might imagine, the division known for processing the lenses and mounting them inside the barrel is vast for the world’s largest independent lens manufacturer. The Optical Elements Processing division is separated into Lens Coating, Lens Centering, Optical Element QC and Washing, Fine Polishing, Edge Painting, Lens Bonding and Lens Caulking.
First up, the lens is centered (to find its optical center) and then the outer diameter is ground away to reach the final lens design. There are between 10-28 lens elements inside a Sigma lens, so it’s crucial for them all to reach a consistent center for high-resolution image quality.
Polishing is critical to achieving a sharp and bright lens, so it’s divided into three stages: Curve Generation, Rough Polishing and Fine Polishing.
As seen earlier, Sigma molds its aspherical optical elements from glass gobs. In this division, the spherical optical elements are ground and polished from pre-formed glass “blanks”. Sigma is able to achieve incredibly high precision in this process, where only 0.05 - 0.1mm of material can be polished away at a time.
Lenses must be washed after final processing and sometimes even between processes. The washing process is a 12-step process that uses fresh water from the Bandai area in Japan, as well as isopropyl alcohol, and ultrasonic pulses to clean away the polishing residue. Some optical elements include glass so soft that it could be scratched by the washing process, so they are also washed by hand.
Now onto lens coatings, and here we saw the workers ensuring that each element is free of dust, residue and blemishes before loading them into “domes” to be carried off to the coating machines.
Sigma uses its proprietary “Super Multi-layer Coating”, which is an anti-reflectance coating applied using a vacuum deposition process. Since, naturally, 4-5% of light is reflected per side of the lens element, and there are 10-28 optical elements per lens, you can see how the loss of light will add up.
The Super Multi-layer coating achieves higher light transmittance per lens element, which enables Sigma to make products with faster apertures. The number of layers of coating range from 1-15, with each layer being only 300-500 nanometers (0.0003-0.0005mm) thick.
Sometimes a group of lens elements needs to be bonded together to correct image defects ("aberrations") that naturally occur in spherically-shaped lenses. The elements are joined using a UV-cured resin, with some of them using a balsam-based resin.
One aspect of lens manufacturing I hadn’t thought about was minimizing reflectance inside the lens barrel. Sigma does this by keeping the inside as dark as possible, and hand-painting the rim of its glass edges with black ink or paint in a process called ‘Sumi-nuri’.
Ryan revealed that the company is working on automated machines for use in this section, though it’s currently such a delicate process that it has to be done by hand. I also had the chance to quiz his brains on Vantablack – the world's blackest material, which uses carbon nanotubes to absorb practically all light, and he told me it was something the company is interested in.
With the lens elements centered, polished, washed and the edges hand-painted, it’s time for assembly in the Lens Caulking area. Here, the optics are press-fitted into lens chambers using high heat and pressure to secure them in place, whil other lenses are screwed into the chamber.
Finally, one of Sigma’s own-made circuit boards is added to the lens.
The finishing touches
The tour concluded with a walk through Sigma’s Assembly Division. All the parts we’d seen thus far are gathered and assembled into the final products. This area is a strict clean room environment, to keep as much dust out of our lenses as possible.
We got to see the Sigma 24-70mm f/2.8 DG DN II Art lens, which is the company's latest big seller, being assembled in front of our eyes with the individual parts assembled into units, which are then adjusted and the resolution tested.
From the window we could see two automated machines: one applying the right amount of grease along the cam barrel grooves, and the other inserting rollers. Both require precision for the best outcome.
All assembled lenses are adjusted and inspected by Sigma's A-1 MTF (Modular Transfer Function) measurement machines, which were developed in-house and are equipped with ultra-high-resolution sensors.
Next up it’s the Quality Assurance division, which uses Sigma's MTF measurement machines from Trioptics to thoroughly evaluate the performance of new lens designs as well as the performance of competitors’ lenses.
The lenses can be evaluated from minimum focus distance all the way to infinity, to get super-accurate performance data across the full focus spectrum.
One of the machines has been in use for around five years and is quite rare, with there only being a few of them in Japan, while another machine was custom-ordered from Trioptics and is the only one of its type in the world.
These machines are used to inspect each lens to ensure it meets Sigma's strict resolution standards, and provide the benchmark scores used by the A-1.
Finally, the Quality Assurance division is responsible for the overall quality control of Sigma products. Since brand image is strongly connected to quality, this division carries out uncompromising and rigorous quality checks; not only on assembled products, but also on individual units as well as pre-production firmware bug checking and camera compatibility checking.
Taking a guided tour through every step of Sigma's manufacturing process was fascinating, educational and a real privilege – and gave us a new appreciation for the true craftsmanship that goes into creating these incredible cameras and lenses. Thank you to Sigma for the great honor of visiting the Aizu facility!
You might also like…
You may also be interested in our guides to the best lenses for filmmaking, the best cine lenses, and the best cheap lenses.
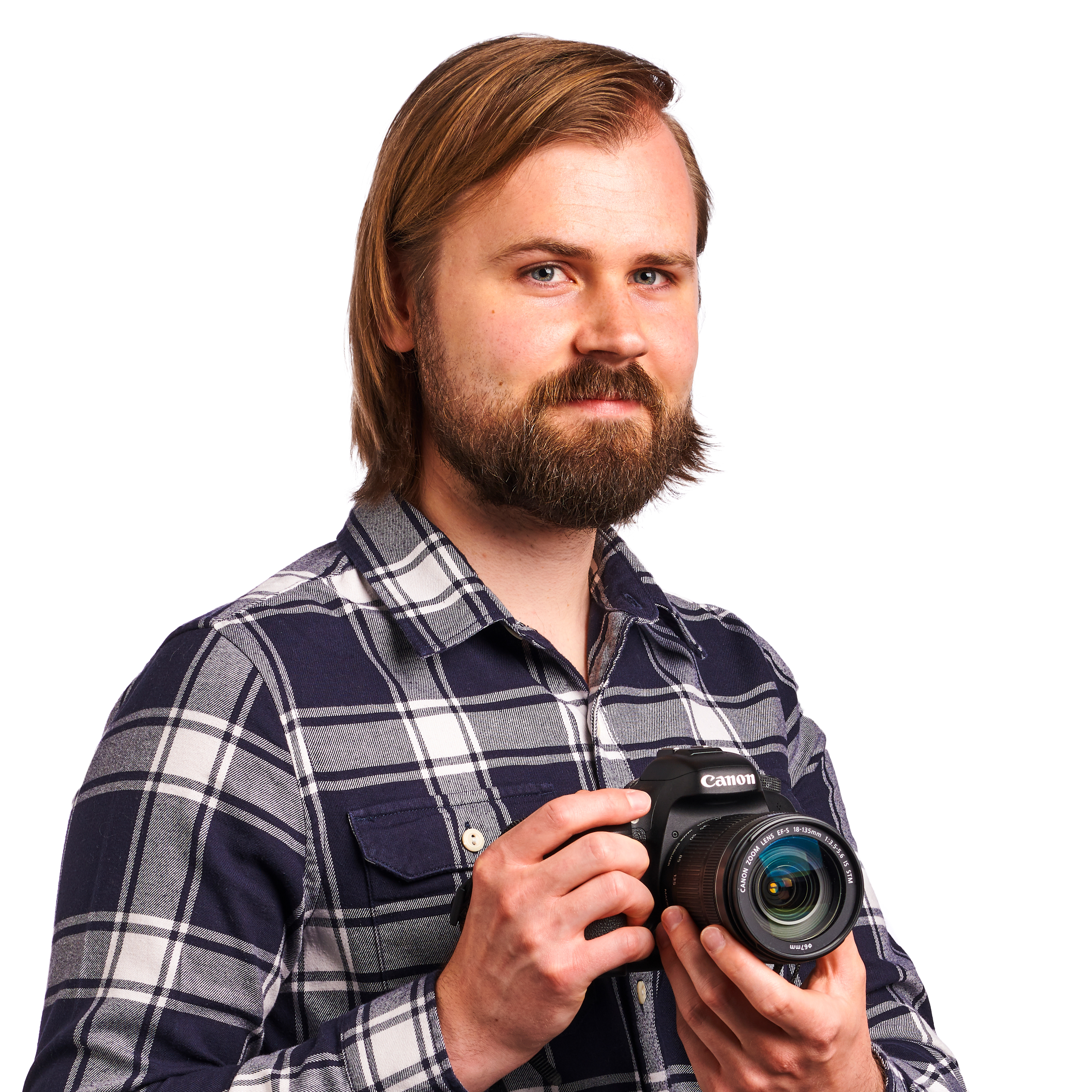
Deputy Editor on PhotoPlus: The Canon Magazine, Dan also brings his technical wizardry and editing skills to Digital Camera World. He has been writing about all aspects of photography for over 10 years, having previously served as technical writer and technical editor for Practical Photography magazine, as well as Photoshop editor on Digital Photo.
Dan is an Adobe-certified Photoshop guru, making him officially a beast at post-processing – so he’s the perfect person to share tips and tricks both in-camera and in post. Able to shoot all genres, Dan provides news, techniques and tutorials on everything from portraits and landscapes to macro and wildlife, helping photographers get the most out of their cameras, lenses, filters, lighting, tripods, and, of course, editing software.
You must confirm your public display name before commenting
Please logout and then login again, you will then be prompted to enter your display name.