20 things you never knew about Canon lenses
We were lucky enough to go on a tour of Canon’s amazing Utsunomiya lens factory in Japan – and this is what we learned
8. Canon's automated lens-assembly machines
These have been developed in-house by Canon and are used for production processes that can be automated rather than carried out by hand. They are checked constantly by their operators, of course, but they have also been designed to be self-correcting, automatically checking lenses as they're produced and making corrections to the process to keep them as close as possible to the design ideal.
9. The Olympics stadium and a plastic bag
Canon's highest-precision lenses for cameras are for the broadcast 4K/8K industry and have a manufacturing deviation of less than 30nm (1 nanometer is one millionth of a millimetre).
That's hard to imagine, so Canon offers an analogy – imagine a lens large enough to cover the Macaraña Stadium in Rio de Janeiro (used for the Olympics), which is roughly 300 metres across. Across its entire surface, this giant lens would demand deviations of less than 0.03mm, which is less than the thickness of a plastic bag!
10. Canon's ideal EF lens
There's more to Canon lens design than you might think.
Canon cites superior optical performance as one of its aims, of course, but it's also targeting competitive pricing, accurate auto exposure, size and weight, unique specifications, ergonomics, operability and usability, durability and rigidity, effective image stabilisation, autofocus performance and movie shooting capabilities. There's a lot more in these lenses than just the glass.
Canon's strategy is to introduce new technologies into its L-series lenses and then work out how to pass these down to the line to its mid-range products and, where possible, to its entry-level lenses.
11. So what’s the hardest lens to make?
We assumed that the complex internal movements of Canon's L-series zoom lenses would make them the most difficult to assemble – the photo above shows all the parts in Canon's 200-400mm zoom – but in fact it's Canon's long L-series super-telephoto lenses that take the most time to assemble – four times longer than zoom lenses like the EF16-35mm f/2.8L III USM. They are assembled by specially trained and skilled Canon workers.
The best camera deals, reviews, product advice, and unmissable photography news, direct to your inbox!
12. Every 16-35mm lens is tested
If you've ever wondered where your money goes when you buy an L-series lens, we might be able to help you there.
We got to see the EF16-35mm f/2.8L III USM production process, where each lens (not just samples) is tested where each lens is individually tested using manually calibrated equipment by hand, using a complex nine-point optical test process.
13. Durability and sensitivity
It's not enough to produce great optical performance just in the factory. Lenses need to be able to maintain this performance through the knocks and hazards and extremes of climate and conditions that photographers put them through.
To that end, Canon places great emphasis on durability and what it calls sensitivity – this is the lens's sensitivity to factory production tolerances, extremes of temperature and the typical bumps and bangs of everyday use.
This sensitivity can be built into the design so that the optical performance is unaffected. One example is the small shock-absorbing bumper rings on the front of some L-series lenses. You probably didn't even know they were there!
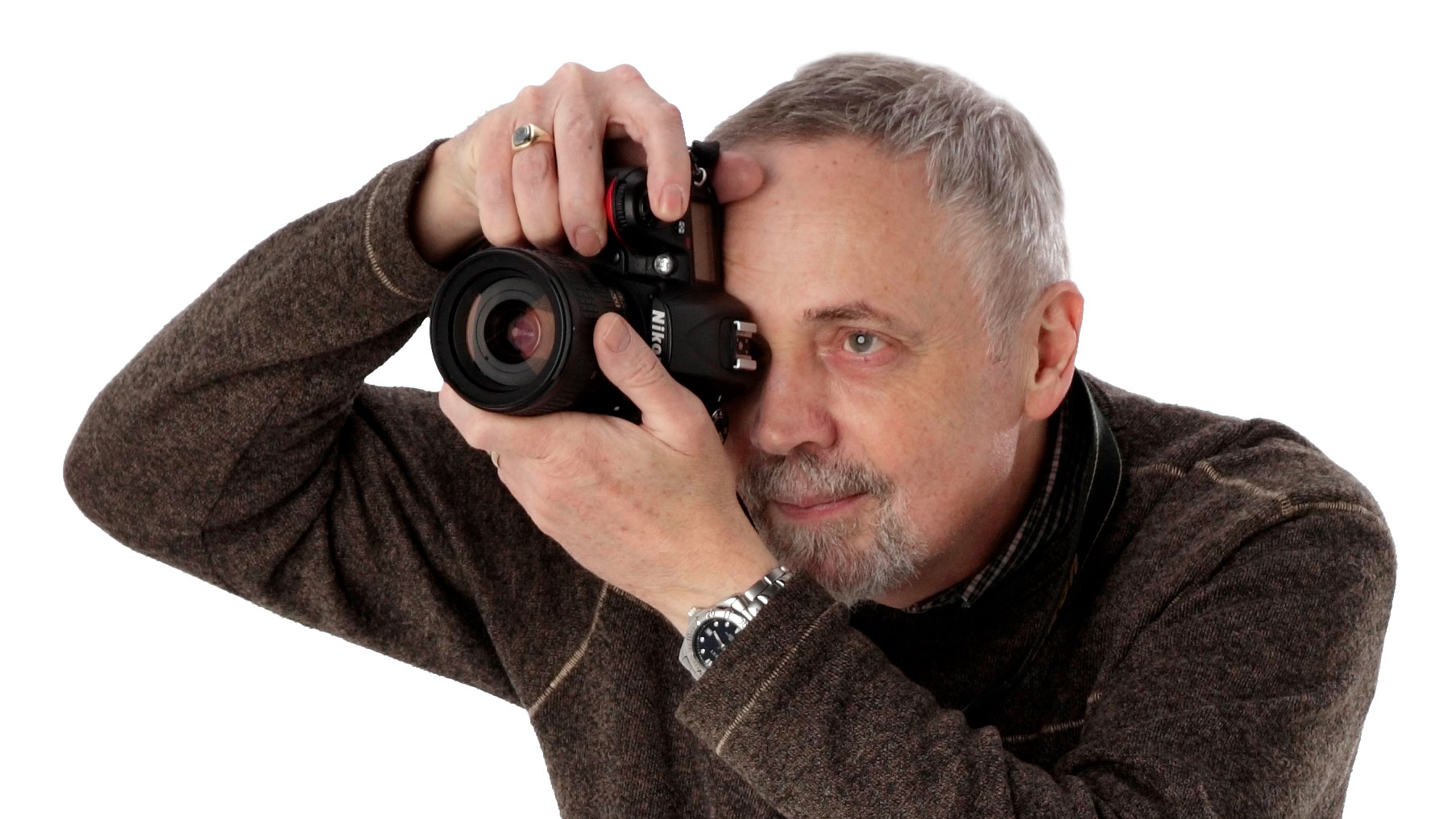
Rod is an independent photography journalist and editor, and a long-standing Digital Camera World contributor, having previously worked as DCW's Group Reviews editor. Before that he has been technique editor on N-Photo, Head of Testing for the photography division and Camera Channel editor on TechRadar, as well as contributing to many other publications. He has been writing about photography technique, photo editing and digital cameras since they first appeared, and before that began his career writing about film photography. He has used and reviewed practically every interchangeable lens camera launched in the past 20 years, from entry-level DSLRs to medium format cameras, together with lenses, tripods, gimbals, light meters, camera bags and more. Rod has his own camera gear blog at fotovolo.com but also writes about photo-editing applications and techniques at lifeafterphotoshop.com